our technical expertise in computer vision, machine learning, synthetic data, and
robotics as well as our purpose-built solutions for the Navy
OVERLAB LLC
Our History
- Founded: January 2020
- SBIR Phase I Grant: May 2020
- SBIR Phase II Grant: July 2021
- Ongoing private sector projects
Who we are
- Founder & CTO: Kevin Murray
- Former Navy civilian roboticist (Naval Surface Warfare Center Dahlgren Division)
- Graduate degrees in mechanical engineering & computer science
- Supported by a highly qualified workforce and network of expert consultants & subcontractors
- Based in Northern Virginia (easily accessible to many DoD/Navy facilities)
THE NAVY CHALLENGE
Equipment maintenance is an enormous effort
- 37,000+ workers across 4 Navy shipyards
- 18,000+ have less than 5 years of experience
- 650,000+ workers across DoD
The Navy is pursuing Augmented Reality (AR)
- Applying AR to guide equipment maintenance workers
- Generating faster repairs and a higher maintenance success rate
The Navy requires AR-guided maintenance solutions that:
- Operate without placing physical markers on the equipment
- Operate without accessing the internet or cloud services
- Operate indoors and in bright sunlight
Expected transition targets
- PMA—260
- PMA—205
OPERATIONAL USE AND IMPROVEMENT
Existing COTS AR-guided maintenance solutions are unusable by the Navy:
- Use physical markers on equipment (unacceptable in some environments)
- Upload equipment data to the cloud (creates cybersecurity risk)
- Only work on rigid equipment without missing parts
Our solutions are purpose-built for the Navy:
- Do not use physical markers on equipment (usable in all environments)
- Run locally (do not need to upload equipment data to cloud services)
- Work on articulating equipment and equipment with missing parts
Our solutions are both improvements and enablers
Improvements:
- Improve effectiveness and value of existing AR-guided maintenance systems
- Deliver accurate results & advanced capabilities vs COTS solutions.
Enablers:
- Provides usable solutions for the Navy and DoD
OUR SOLUTION: EQUIPMENT STATE RECOGNITION
What is “Equipment State Recognition”?
- For AR guidance to work, holograms must point to equipment locations from the user’s perspective
- At a minimum, the system must estimate the equipment pose relative to the user
- To handle equipment with missing or moving parts, we must also handle assemblies and articulations
Our Core Capabilities
- Pose Estimation
- Assembly Recognition
- Articulation Recognition
- Multiple Equipment Recognition
The Navy requires AR-guided maintenance solutions that:
- Recognizes equipment state by combining 3D CAD models with AR sensor data
- Runs on local systems, not cloud services
- Uses high-fidelity synthetic data
- Uses visible light to allow for dark/reflective surfaces, small parts, and usage in sunlight
- Recognition neural networks are generated automatically from equipment geometry – without equipment texture information
Our Performance Targets
- Pose Estimation Target: Obtain a position error of 5cm and 5 deg at the 90th percentile
- Assembly Recognition Target: Predict the presence of equipment parts with a 95% accuracy rate
- Articulation Recognition Target: Obtain a position error of 5 cm and 5 deg at the 90th percentile - for each articulating joint
OUR CURRENT STATUS
Rigid Body Pose Estimation
- Error rate: 4.1 cm and 7.9 deg at 50th percentile
- We expect to hit target benchmark in practice by using multiple images and viewpoints
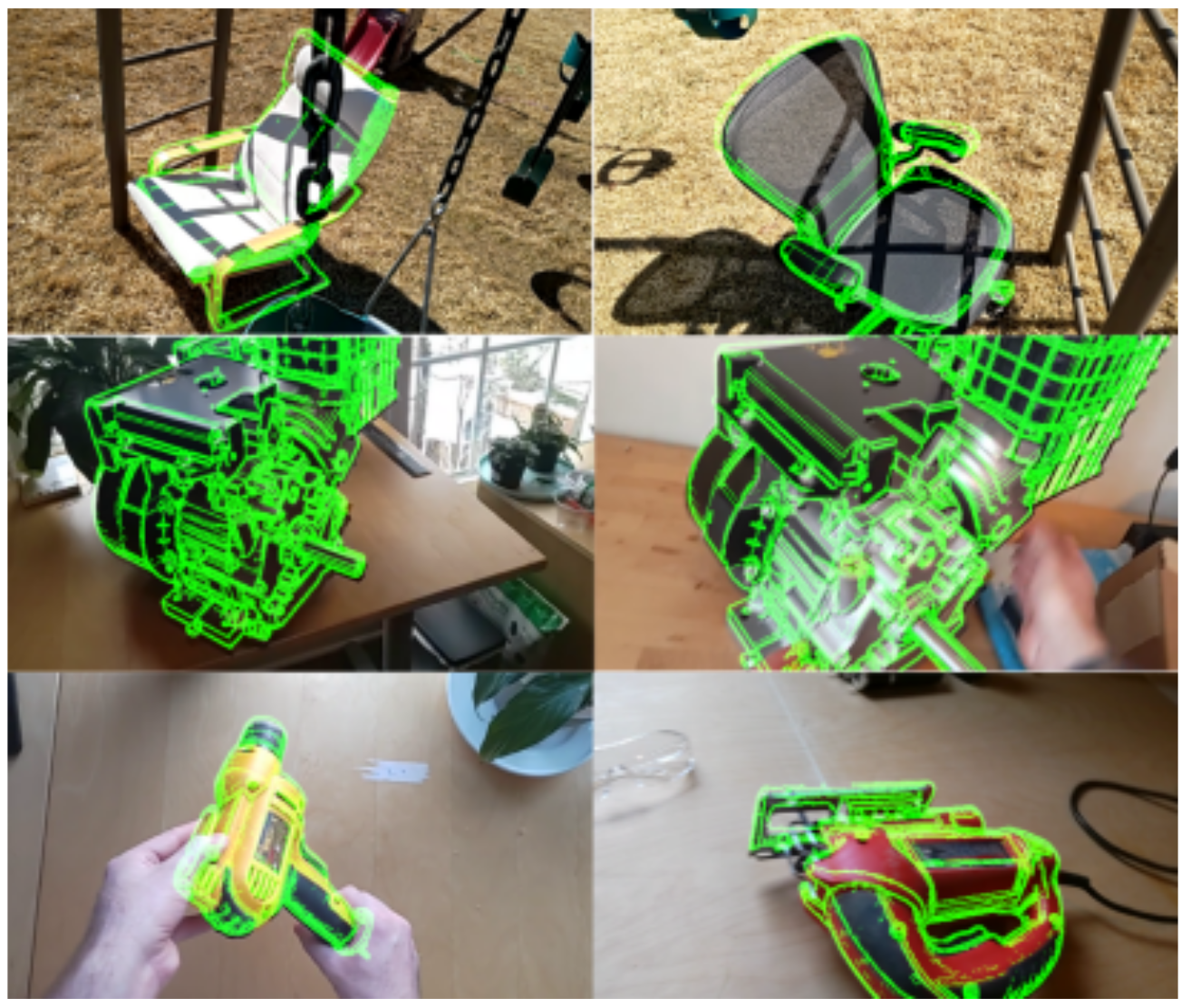
Assembly Recognition
- Test on arbitrary assembly states and synthetic data
- Assembly state accuracy: 79%
- Error rate: 6.9 cm 5.0 deg at 50th percentile
- Test on real assembly (133-part Briggs and Stratton 10 HP engine)
- Part recognition accuracy: 90%
Estimated Pose And Estimated Assembly State
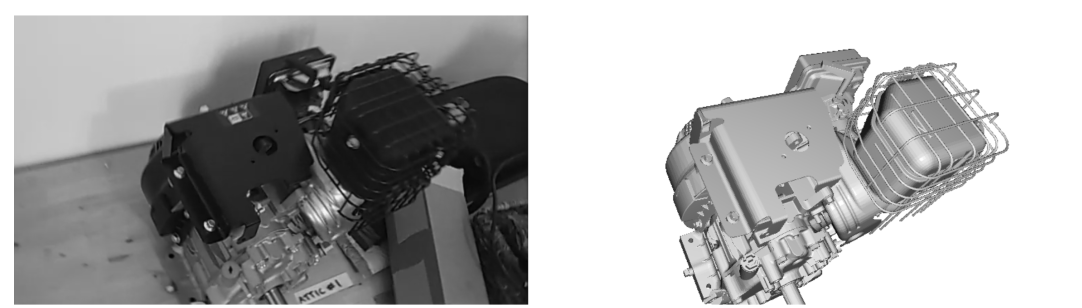
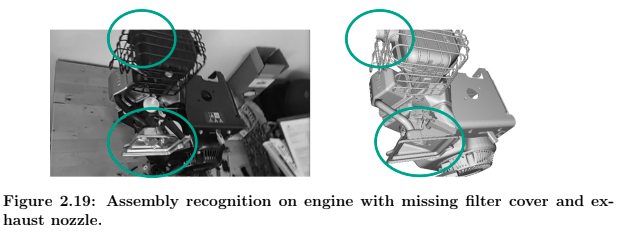
OUR STATUS: PROJECTED TECHNOLOGY READINESS LEVEL (TRL)
At the end of Phase II Base
Rigid-body pose estimation
TRL: 6
Notes: Make prototype near desired configuration in terms of size and weight, and test in relevant environments.
Assembly state recognition
TRL: 5
Notes: Test in relevant environments.
Kinematic state recognition
TRL: 5
Notes: Develop prototype and test in relevant environments.
Multiple equipment
TRL: 5
Notes: Develop prototype and test in relevant environments.
At the end of Phase II Option
- All capabilities at TRL 6 - 7
- Prototypes designed near desired size and weight
- Prototypes tested in relevant environments
FEATURES - ADVANTAGES - BENEFITS
Local Systems
Advantage: No cloud services or internet connection.
Benefits: Less cybersecurity risk.
Computer Vision
Advantage: No physical markers on equipment.
Benefits: Works in more environments.
Automated Recognition
Advantage: No real-time video chat with experts.
Benefits: Faster, broader, more efficient maintenance.
Visible Light Cameras
Advantage: No sensors that fail in bright environments.
Benefits: Works in bright light (e.g. sunlight)
Equipment Assemblies
Advantage: Identifies missing parts and defines state even when parts are missing (COTS options cannot).
Benefits: Fix equipment with missing parts.
Kinematic Recognition
Advantage: Recognizes the state of moving parts in equipment like joints (COTS options cannot).
Benefits: Fix equipment with moving parts.
LOOKING AHEAD: TRANSITION TO FLEET & MARKET ANALYSIS
Existing COTS AR-guided maintenance solutions are unusable by the Navy:
Resources We Need to Transition
- Funding to take us from TRL 6-7 to a commercial product
- Access to Navy facilities to perform operational testing
Our Primary Transition Advocates
- Michael Confessore — CREATIVE Lab, NAWCAD Lakehurst
- Dustin Huber — Navy STP
Market Analysis
Significant Commercial Opportunities
- Construction, and Industrial Manufacturing and Maintenance
- License technology to larger AR system integrator (e.g. Microsoft, PTC)
Alternative Uses
- Equipment fault detection (identify anomalies)
- Equipment diagnostics (identify the cause of faults)
TRANSITION & PARTNERSHIP POINTS: KNOWN & UNKNOWN
Equipment maintenance is an enormous effort
- PMA—260: Manages acquisition and lifecycle support of aviation equipment.
- PMA—205: Develops training programs for equipment maintenance.
However, we suspect there’s a broader set of applications we have not yet identified:
- Our solutions can help many groups using COTS AR systems (e.g. Microsoft, PTC)
- Equipment state recognition can support many activities related to equipment maintenance
- Combining CAD equipment data with AR sensor data has applications outside of equipment maintenance
As such, we are currently seeking additional relevant solicitations and writing proposals
CONTACT US TODAY!
TAKE THE RIGHT NEXT STEP WITH OVERLAB
Located in: Clifton, Virginia (Eastern Time Zone)
Kevin Murray
CTO, Overlab LLC
Email: [email protected]
Phone: (703) 899–1842
or click below on "Request A Demo"
55% of small business owners believe their fleets will be fully autonomous in 20 years.
(Global Nissan News)